Laser hardening
When you want hardening with minimal shape distortion
Laser hardening is a surface hardening method with high precision where only selected areas are hardened. It offers several advantages, such as a hard surface with retained toughness in the rest of the material, as well as minimal shape distortion after hardening. Thanks to the laser’s high efficiency and the fact that only the needed area is hardened, the process also results in a very low carbon footprint. Laser hardening can replace many other hardening methods, such as case hardening, induction hardening, or various types of nitriding, and can be performed on all hardenable materials. Compared to induction hardening and case hardening, the shape alterations are significantly smaller, minimizing the need for post-processing. Typically, the hardening depth ranges from 0.2 to 2.0 mm, which is considerably larger than with nitriding. Surface hardness is comparable to other hardening methods and depends on the chemical composition of the base material.
Referenscase
Moulding tool Uddeholm Rigor
Moulding tool manufactured in Uddeholm’s Rigor steel, which with an excellent combination of toughness and wear resistance is well suited for laser hardening. The working surfaces are laser hardened to approximately 60 HRC. The tool is completely machined before laser hardening and is used directly without any further processing afterward, as is normally common with other hardening methods due to shape distortions.
Series Product Ductile Iron EN-GJS-600-3
For Osby Mekan AB, we laser harden the series product Axle Mid-Joint that is used in Dynapac’s articulated road compactors. The base material is ductile iron EN-GJS-600-3, and the surface that undergoes laser hardening is a h7 bearing surface, diameter 180 mm. Laser hardening is performed directly on the finished h7 bearing surface as the final step. The hardening depth is set to approximately 1.0mm. Previously, the product was induction hardened, but it required machining after hardening due to reach the tough tolerance on the bearing surface.
Machine Part Toolox®44
Machine part – hammer manufactured in Toolox 44® material. Laser hardening is performed only on the wear-prone surface, thereby maintaining the properties of “High Base Hardness” and “High Toughness”. An unbeatable combination in this type of process. The hardening depth is set to approximately 1.7mm, and the surface hardness amounts to approximately 57 HRC.
Guide Rail 1.2312
For our customer Skoogs Mekaniska, we laser harden, among other things, guide rails for material transport in a hot rolling mill. The surface has a width of 100mm and is laser hardened with 3 hardening tracks to approximately 55 HRC and with a hardening depth of approximately 2.0mm. Due to the shape requirement, the opposing side is also heated , thus providing the customer with a straight and flat product. Material grade 1.2312 is a toughened tool steel with a base hardness of 280-320 HB, supporting the laser-hardened surface which, in turn, can withstand significant surface pressures.
LASER- SURFACE HARDENING
About laser hardening
The goal of all surface hardening methods is to achieve a hard surface layer while maintaining a ductile core.
During laser hardening, the high energy density of laser light is utilized to heat the specific surface to austenitization temperature, typically between 900-1200 degrees Celsius. The heating time takes only a fraction of a second, and the laser light is directed over the surface of the component using, for example, a robot with a feed rate ranging from 1-24 mm/s
The short heating time allows the surrounding cold material to rapidly cool the heated area, thus hardening the surface. The hardening depth is determined by the feed rate and temperature and typically ranges from a fraction of a millimeter up to 3.0 mm. The hardened zone is well-defined against the unaffected base material. Hardness decreases rapidly at the boundary between hardened and unhardened material.
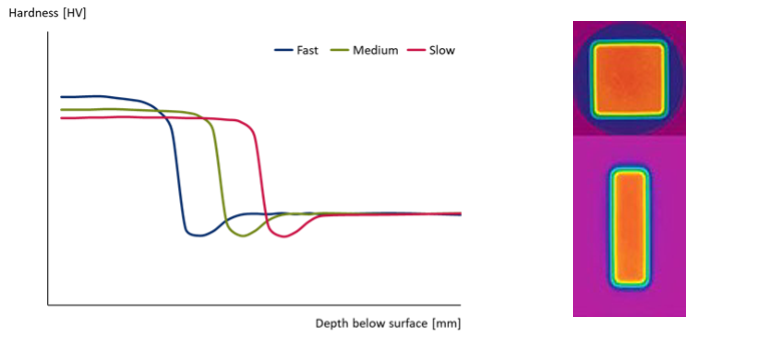
Examples of how hardness and hardening depth can be controlled with the laser’s speed
Examples of different laser spot geometries
With different optic configurations, the laser spot geometry can be selected, usually as square or rectangular, depending on the object’s shape and customer preferences. The size of the rectangle can range, for example, from 2mm up to 60mm in both directions.
If larger areas should be hardened, the hardening must be done with overlapping tracks. In the overlapping zone (approximately 1.0 mm), a slightly lower hardness is obtained due to tempering.
Integrated into the laser system is a pyrometer that continuously measures the surface temperature throughout the process and adjusts the laser power accordingly. Thanks to the pyrometer, a stable and high-quality hardening layer is always maintained. The factors that make laser hardening particularly competitive include the limited total heat input compared to any other comparable method. The deformation of the workpiece after hardening is minimal, and it is possible to use hardening as a final step in the manufacturing chain. Scrapping or additional manufacturing steps to correct dimensional changes due to deformations can be reduced or eliminated. This represents a significant step forward in the pursuit of cost reductions
At LaserTool, we can handle both complex components and simpler straight details. For more complicated 3D geometries or extensive work, programming, which controls the robot and the process, is typically done offline. For this type of job, 3D CAD models of the detail to be laser hardened are required.